We’ve Gotta Say It, The InvisiPac Tank-Free Hot Melt System is Pretty Cool!
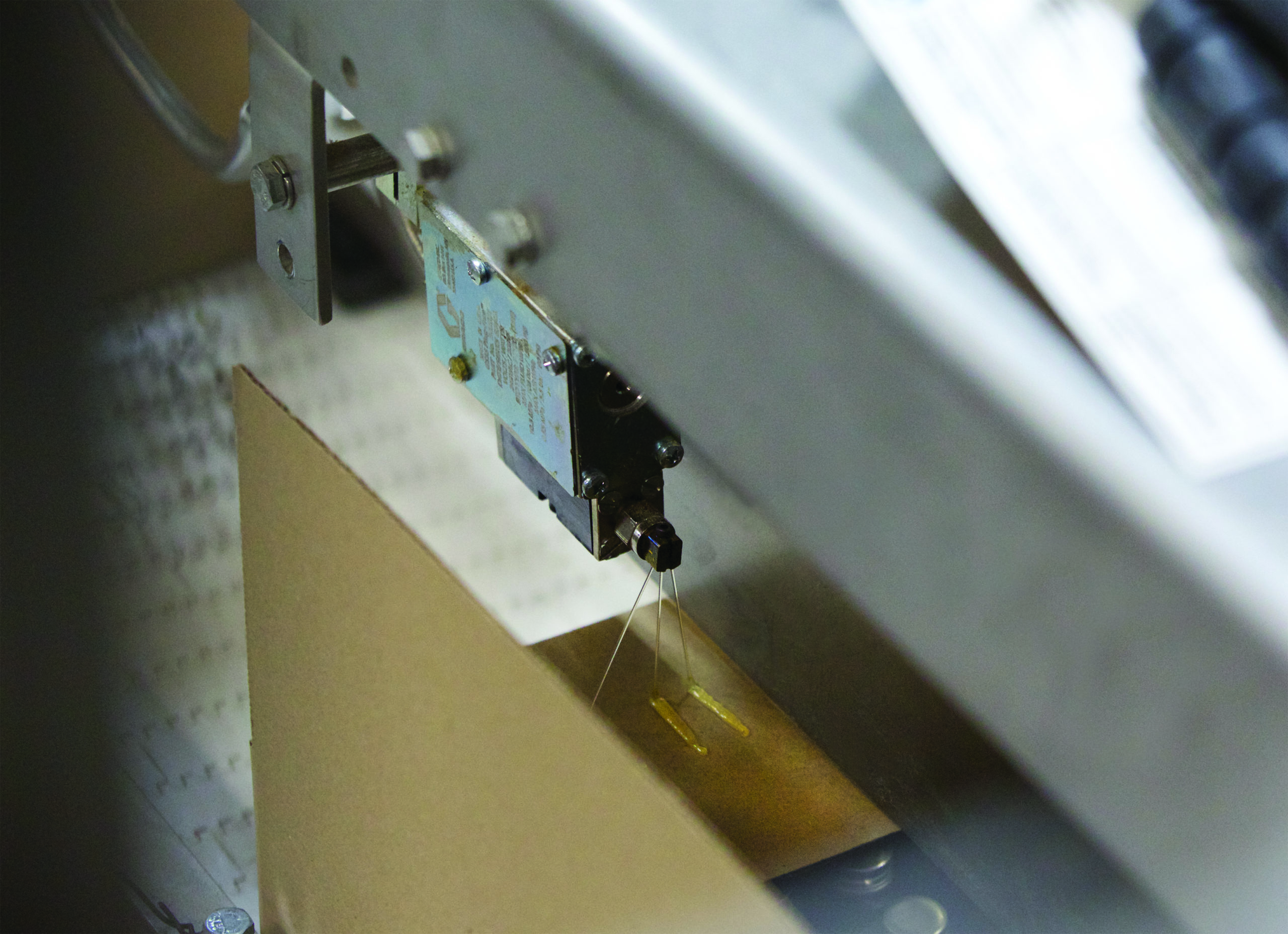
Safety, savings, and sustainability – the technologically advanced InvisiPac tank-free hot melt adhesive delivery system has it all. Compared to InvisiPac, other conventional hot melt equipment doesn’t measure up. So, whether you are looking to reduce energy consumption, eliminate costly downtime, or amplify adhesive savings, the Graco InvisiPac system meets today’s packaging applications’ varied needs and demands.
An Emphasis on Employee Safety
Many traditional systems require employees to refill hot melt tanks manually, exposing them to 350°F molten adhesive. In the refilling and scraping process, there is the potential for splashes to occur, which can cause severe burns. Opening the tank also exposes workers to toxic fumes, irritating the lungs and eyes. Additionally, glue pellets often spill onto the floor during manual refilling, posing a potentially dangerous slip hazard.
To combat these safety concerns, Graco engineers designed a truly tank-free, melt-on-demand system standard on every InvisiPac machine. Utilizing an automated feed process with a “first-in, first-out” approach, when adhesive falls to a certain level, the amount of adhesive needed is sucked from the adhesive container directly into the melter. As a result, employees have no direct contact with the hot adhesive and your line is always running.
Adhesive Savings You Can Count On
Rising adhesive costs are an unfortunate reality. Using less glue is one way to mitigate inflation. The following study is a perfect example of how the InvisiPac utilizes less glue.
A large global snack food company’s packaging facility realized substantial savings after switching from Nordson to the Graco InvisiPac System. Factory data revealed a 62% decrease in adhesive use from 0.50 grams of glue per carton to 0.19 grams of adhesive with InvisiPac.
The facility in this example produces 1.88 million cartons per year. Do the math! That’s a significant amount saved on adhesive over a year, which allowed real, quantifiable dollars to be invested in other areas within the factory.
Lower Energy Use Every Day
The InvisiPac Tank-Free system takes just 10 minutes to reach operating temperatures after start-up. Conventional hot melt equipment can take up to 50 minutes to reach operating temperature. InvisiPac’s industry-leading start-up time results in a 48% reduction in energy consumed during start-up.
Some plants keep their conventional hot melt machines running around the clock to avoid prolonged start-up times, even when not in use.
The InvisiPac system also features auto shut off after an hour of idle time, resulting in 26% less idle time energy use.
Reduced start-up and idling add significant energy savings every day, which helps the environment and benefits your bottom line.
We’d love to get you on the road to reduced energy consumption, unnecessary downtime, AND adhesive savings. So, contact our adhesive experts today for a demo of the InvisiPac Hot Melt System!
Hot Melt System Comparison Chart
Graco’s InvisiPac tank-free hot melt system outperforms all existing tank and tankless systems on the market. The InvisiPac system delivers guaranteed savings, optimizes production, and improves safety with a true melt-on-demand design.