Hot Melt Viscosity? Boiling Pasta? 40% Adhesive Reduction?
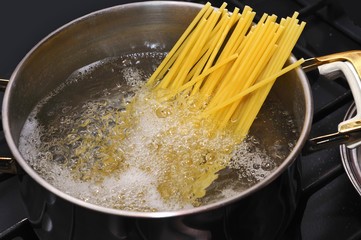
Do you know the impact of your hot melt viscosity can have on your production costs? Improper control of the viscosity can increase your glue usage by as much as 40%.
Most people have made a pot of pasta and know that the first step is to boil a pot of water. Next, you add your pasta to the boiling water. Why is it when you add the pasta, the water stops boiling? That is because the lower temperature of the pasta shocks the boiling water and lowers the temperature below the boiling point. The same phenomenon occurs in your hot melt equipment.
Let’s say your equipment is set at 350°F. The entire tank is molten and up to temperature. Your production line is running and you are dispensing adhesive onto each box. As the glue is consumed, your operator needs to add more adhesive into the tank so that you do not run out. Just like the pasta example, the large amount of room temperature hot melt that is added will shock the molten adhesive and lower the temperature.
Temperature has a key role in the viscosity of your hot melt adhesive. Each product has a unique viscosity curve, but the one consistency is that the product’s viscosity increases when the temperature is lowered.
So how does this impact your hot melt usage? We know that a product that is higher in viscosity does not flow as well and will require more pressure to force out of the end of your system. Your production line needs to continue to successfully run no matter the viscosity of the hot melt. Your skilled operators ensure that is the case and have identified that to get enough adhesive on the box to make a successful bond, they need to increase the pressure to the pump when the viscosity is higher. Then, over time the temperature in the tank rises, the viscosity of the glue goes back down, and your production line continues to run successfully.
However, the pressure to the pump is still at the elevated level needed to run successfully at the higher viscosity. Now that the adhesive viscosity is lower and it is flowing easier, the equipment is applying much more adhesive than is needed to successfully seal the box shut. In Chicago Glue & Machine’s experience, most production lines experience this exact cycle of viscosity multiple times a day and causes them to use much more adhesive than needed.
We have a proven solution to keep the hot melt viscosity consistent throughout the entire day of production. It has helped some of our customers reduce the amount of hot melt adhesive that they consume by 25%-40%. Please contact your CGM representative to discuss if this could be a solution for your unique adhesive application.