Are You Looking to Reduce Costs and Increase Adhesive Mileage?
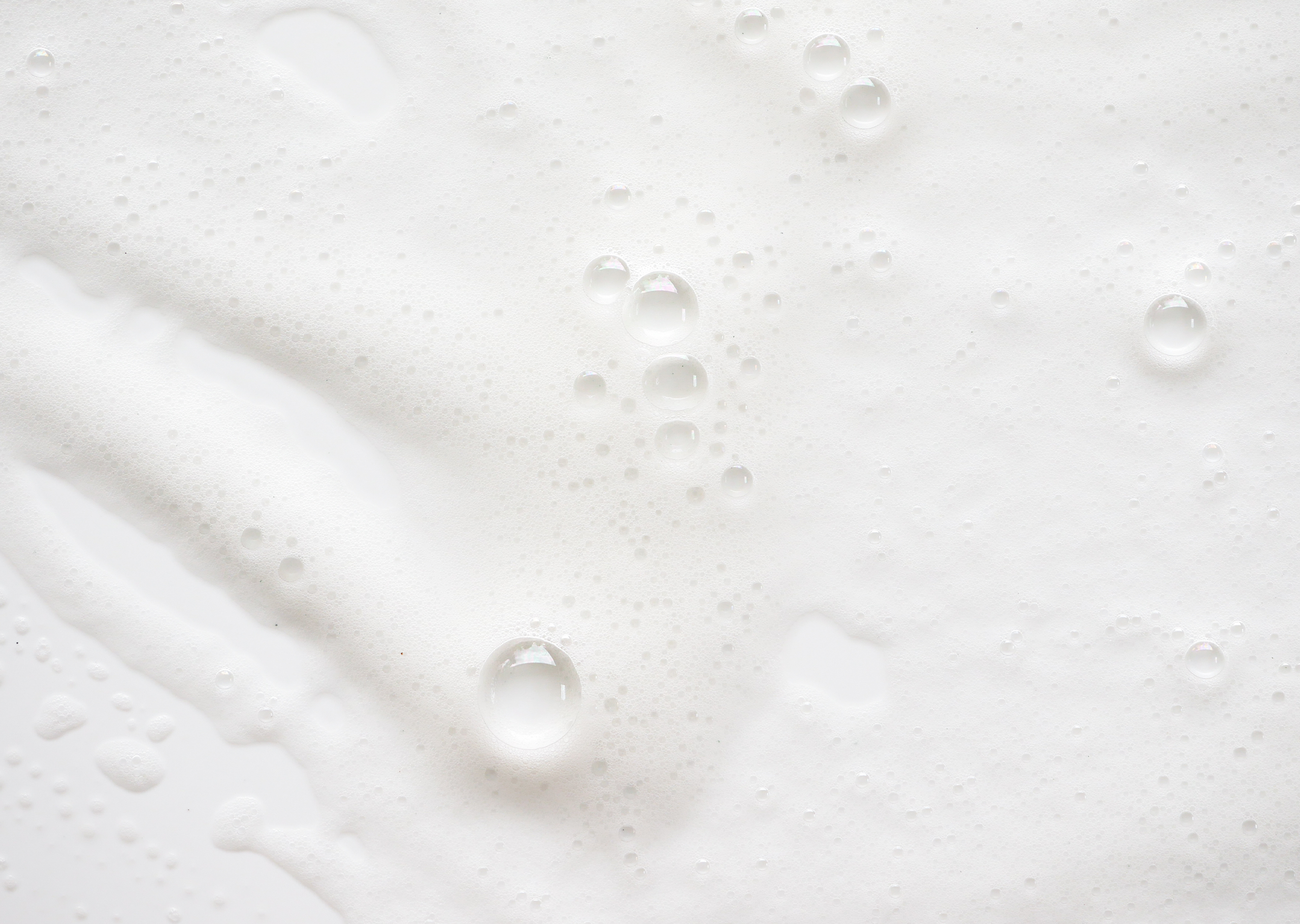
We are always looking for ways to help our customers improve efficiency, whether with the glue and equipment we supply or working with them to optimize their adhesive operations and reduce downtime.
For large-scale, high-volume applications that use water-based adhesives, foaming may be a way to cut costs and increase output.
The principle behind adhesive foaming is relatively simple; foaming reduces adhesive density, increasing its yield. So how does it work?
A mechanical mixer or foamer incorporates a steady volume of air into the glue. The mixer or foamer is part of an adhesive foaming system that ties into the existing adhesive application equipment. As the air is blended into the adhesive, it displaces some of the water, foaming the adhesive. The foamed adhesive is then directed to the application point and utilized in the same way as the non-foamed adhesive.
The increased mileage achieved from foaming can reduce adhesive costs by 10 – 30 percent. However, the benefits of adhesive foaming extend beyond cost savings.
As air is introduced into the adhesive, the amount of water in the process is reduced proportionately, which helps eliminate several moisture-related problems. Lay flat is improved and buildup on cutting surfaces is minimized.
Faster set times and improved holdout on recycled and highly absorbent substrates are achieved due to the foamed adhesive’s higher viscosity / lower density.
Other benefits of adhesive foaming include:
- Less warp
- Better bond
- Improved open times
- Increased wet tack
- Reduced adhesive usage
For foaming to work correctly, the defoamer must be removed from the adhesive during the manufacturing process.
Many factors need to be assessed when considering the incorporation of adhesive foaming. Contact the Chicago Glue and Machine experts to determine if foaming is appropriate for your application.