Metallocene Hot Melt: What you need to know
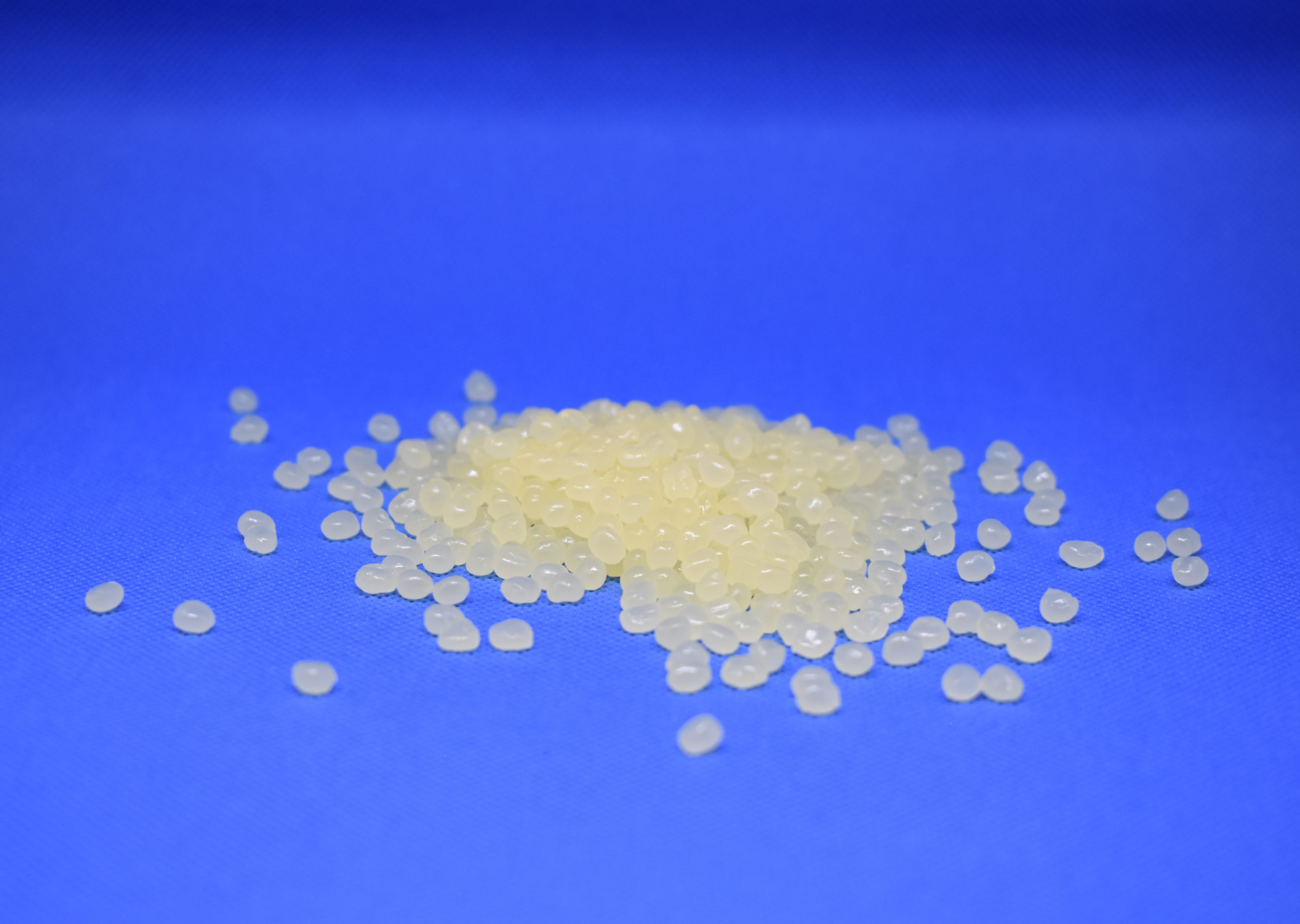
The versatility of hot melt adhesive makes it a popular choice for many packaging applications. Two polymers, ethanol vinyl acetate (EVA) and metallocene are the backbones of the hot melt industry. EVA’s have been around longer and are often selected by default. But metallocene offers some distinct advantages. In this article, we will take a closer look at what sets metallocene apart.
More mileage
The polymers don’t impact the viscosity; therefore, metallocene and EVA have relatively the same viscosity. Most viscosities are manipulated by other additives in the adhesive formula, like wax or oil. However, metallocene is less dense than EVA hot melt. So, pound for pound, you can glue more – or get more mileage – with the same amount of adhesive.
Metallocene is for you if you are using a significant amount of adhesive in your packaging or assembly operations.
As adhesive sits in a tank, it degrades and breaks down, causing an increase in viscosity. With increased viscosity, more pressure is required from the pump to put out the same amount of material. When boxes don’t seal properly, operators may increase the pressure to the pump to get it to dispense more glue. But that doesn’t address the root cause of the issue – the thicker adhesive in the tank. Eventually, the tank will “turn over” and be filled with glue at the original viscosity, but the operator may not adjust the pump back to the previous setting. So, more glue is being output than needed. Adhesive is used in waves, not at a steady level.
Withstands the heat (and cold)
Because metallocene does not absorb oxygen like EVA, heat does not have as significant an impact. In turn, it melts more cleanly in the tank.
Heat resistance is important because metallocene can remain at temperature for longer than EVA adhesives without charring or burning. This means you can keep the tank on, even if you are not using it for some time, which means less downtime waiting for the tank to heat back up. And less downtime means more uptime or production.
Metallocene is also more resistant to cold and can be used for freezer/refrigerator food product applications.
Cut down on char
Inevitably, contaminants get into the glue. At 350°F, the typical application temperature, those contaminants will begin to bake and turn into char. Hot melt systems have several filter points. If those filters become clogged or blocked, the adhesive output is compromised. If the char is fine enough to make it through the filters it travels to the nozzle. The flake or char can block the nozzle opening, so no glue is dispensed. Consequently, boxes are not sealed.
Metallocene adhesives were designed to withstand degrading and the subsequent buildup of char as it sits in the tank.
Improved equipment health
The use of metallocene will improve equipment health in the long and short run. For starters, consistent viscosity means less work for the pump. Reduced char means you do not have to change filters as frequently. Additionally, with metallocene, you are less likely to have to change modules and nozzles as frequently.
More maintenance means more cost and machine downtime, which also has a cost associated with it.
You may think it only takes 15 to 20 minutes to change a filter; no big deal. But that is 15 to 20 minutes of output lost. And if you have multiple production lines, the cost and time is compounded.
If you’d like to learn more about metallocene and how it can help your productivity, contact us today!