How to Protect Yourself from Material Allocations
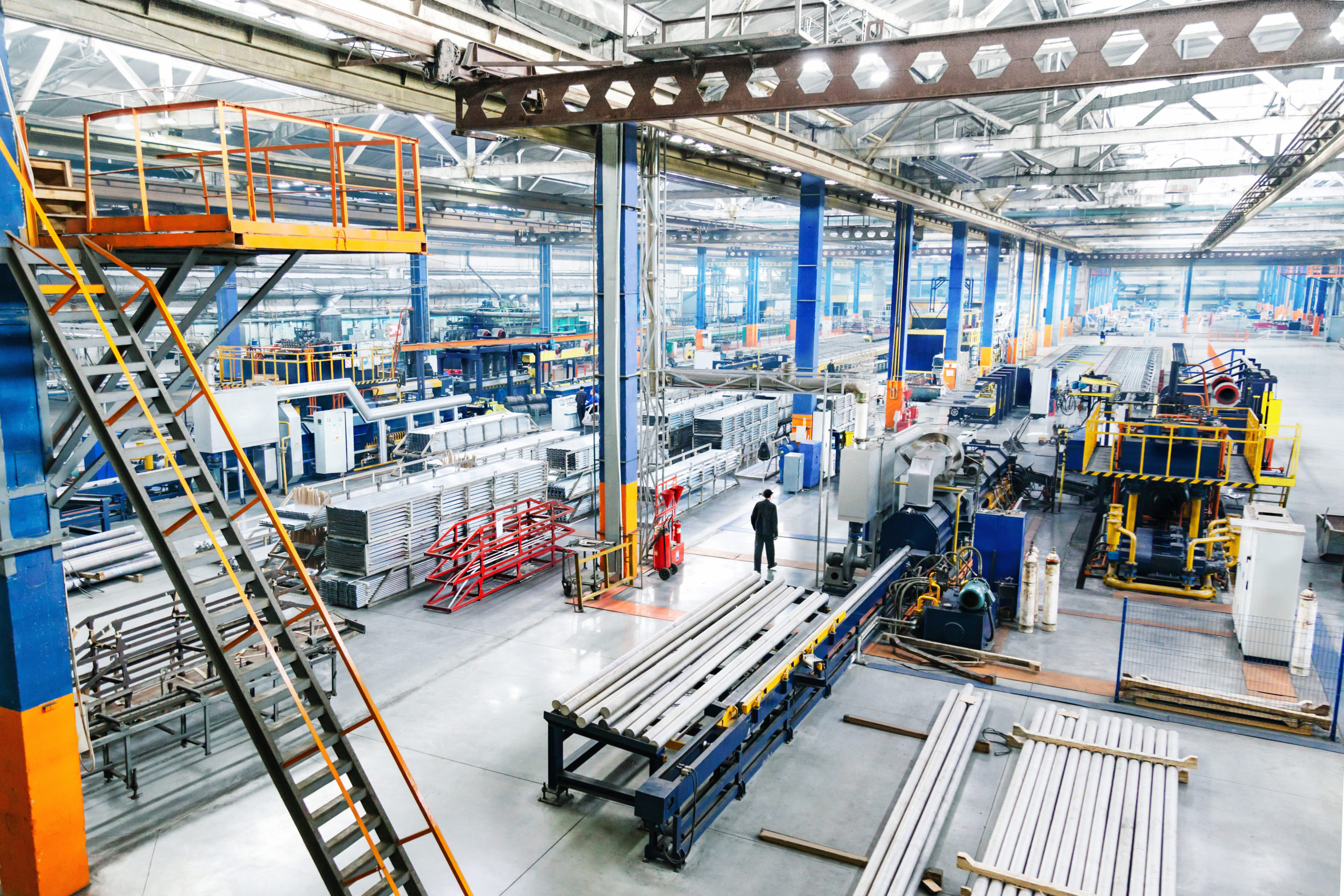
Were you one of the many manufacturers impacted by material allocations over the past year? Because of disruptions to supply chains due to the ongoing COVID-19 pandemic, many raw material suppliers were forced to limit the amount of inventory they could sell to customers. In the adhesive industry, we found that inventory was incredibly limited from February to May, with some lingering items still presenting challenges. As a distributor, we had to work closely with our suppliers to help get the adhesive our customers needed into their hands. While the supply chains have balanced out over the last few weeks, we thought it would be helpful to share what we learned in this process to better prepare you in case we’re faced with these challenges again.
Build a strong relationship with your supplier
From our standpoint, our relationship with H.B. Fuller (HBF) made a huge difference in how we navigated inventory issues. HBF is one of the largest consumers of raw materials, so their buying power helped them acquire as much as they could. And as a result, CGM had access to a portion of their inventory which we could then circulate to our customers.
With a solid relationship built on trust, they knew when we were asking for product, we truly needed it and we weren’t “crying wolf.” This same scenario was true for our customers – we were able to speak candidly to determine what was absolutely essential so everyone could get what they needed.
Be a big fish in a small pond
The sad reality is that due to their size, many of our customers would not have acquired product if they were buying direct from the manufacturer. Larger companies would have taken priority over smaller ones. So, if you’re on the smaller side, working with a distributor is the way to go. We can pool all of our customers together to have a larger overall buying power, thus the manufacturer is more motivated to keep us happy.
Do not stock legacy products
If you’re using an older “legacy” adhesive, now is the time to phase it out. When a SKU is old and fewer customers are using it, it takes a back seat to newer, higher volume products. Try to avoid putting yourself in a situation where the product you need the most is one that will not be prioritized up and down the supply chain.
Use a product that is stocked by a distributor
Most manufacturers do not stock excess inventory. Instead, the adhesives are produced once they have been ordered. That means when raw materials are allocated or short, there is no buffer of inventory to protect you. On the other hand, if you purchase your product through a distributor, chances are that the product is in stock on the distributor’s shelves. That is how we were able to continue supplying many of our customers with the adhesives they needed – we had inventory ready to go!
Let’s put it into perspective: once we found out about the material allocations, we had roughly two months’ worth of inventory available for certain products. So even if the entire market went to zero pounds available, our customers would have been running two months longer than everyone else!
CGM is Available 24/7/365
We know you never want to find yourself in a world without glue! As supply chains continue to ebb and flow, please don’t hesitate to contact us if you run into any issues. Not only do we have inventory on our shelves, but we’re available 24/7/365 to help keep your production line up and running.