Have No Fear, CGM Adhesive Audit Pros Are Here!
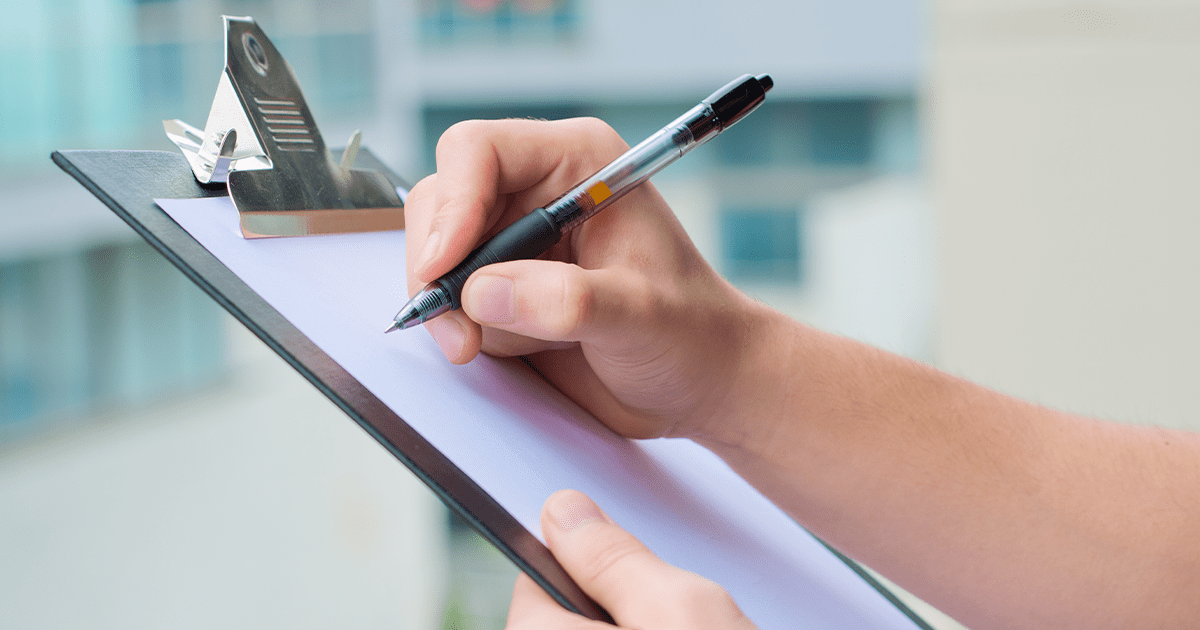
You know we love adhesives, but we also get the warm and fuzzies when we think of audits too! No, not the kind of audit that requires an accountant. We’re talking adhesive audits that are intended to save you money and unplanned downtime.
We Go Beyond the Glue!
When most adhesive suppliers conduct audits, they typically look at just the glue side of the equation. How much glue is going on to the box? What is the weight of the glue? What is the bead length? How consistent is the adhesive?
At CGM we take it one step further. We don’t just look at the glue; we look at the adhesive equipment too, providing a comprehensive Application Audit.
Along with the adhesive details noted above, CGM’s Application Audit Report includes machine settings as well as part numbers for the guns, filters, hoses, modules, nozzles, solenoids, and other relevant equipment used in the production line. We grade the condition of the equipment to help identify any potential maintenance needs.
Best of all, you don’t have to interrupt your operations. The audit is conducted while your equipment is up and running.
Identifying Efficiencies is the Name of the Game
Once the adhesive details have been captured, our adhesive experts go to work uncovering opportunities for efficiencies in cost, inventory and quoting.
We look at the portion of the package to be sealed and the amount of glue being applied. For example, the flap of the box that you are gluing is 6 inches, and your equipment puts down a bead of glue that is 4.5 inches and weighs one gram. Based on our extensive experience we know whether you need that much glue to seal a box of that size. Our audits will outline recommended adjustments and the corresponding reduction in adhesive consumption, which results in adhesive cost savings.
By establishing a baseline of how much glue is needed for your application(s), with regular audits you can track to make sure you are at pace with estimated usage. If the amount changes, it is typically an indication that something has changed with the equipment. By referring to previous reports we can compare what has changed and why costs are increasing.
Regular audits also help with inventory management. You know how many pieces come off your production line and if you know how much glue you are putting down on each piece, you will know exactly how much adhesive you need to inventory.
In the contract packaging world, knowing how much glue is being put down per piece and how much that glue costs can help the sales team provide more accurate quotes.
Avoid Glue-mergencies! Audit Often!
CGM recommends auditing your adhesive system at least once a quarter. But for high-volume applications consider monthly audits.
The adhesive equipment shouldn’t be changing that much. So, if you are having issues with the equipment starting and stopping and production line interruptions, the glue may be a factor. Frequent audits to check that the settings are still the same will be beneficial.
Machine operators may tweak and adjust settings that have unintended consequences when it comes to adhesive applications.
As audit experts, we’ve seen it all! For example, at times preventative maintenance can be lax causing filters not to be changed. Then the filters get clogged and the operator notices that they are not dispensing enough adhesive to seal the box shut causing the operator to turn up the pressure on the pump. This causes more and more char to build up and then no glue is dispensed. So the operator thinks it’s the glue that’s not working when it is actually an issue with the equipment.
Another example occurs when a maintenance technician makes an adjustment that inadvertently changes the compression on the box being sealed. And now there are boxes coming down the line that are popping open. Again, you might think the glue isn’t working.
In both scenarios, audit reports will help identify if something has changed. In the case of the clogged filter, you might see that the pressure is 30 psi higher than when the audit was conducted. You can then drill down to the root cause of why it was changed.
Our “hot” take? Regular audits comparing the system to the established baseline settings help determine if the settings need to be reset or a new baseline established.
It’s as Easy as Asking
For CGM customers, Application Audits are part of our service offering. All you have to do is ask and our experts will be there! New customers receive an initial audit to establish a system baseline and receive an audit report each time an Application Audit is conducted.
Not a CGM customer but would like an Application Audit? Contact Adam Norton to learn more and get our experts to your facility!