Glue Fail in the Wild
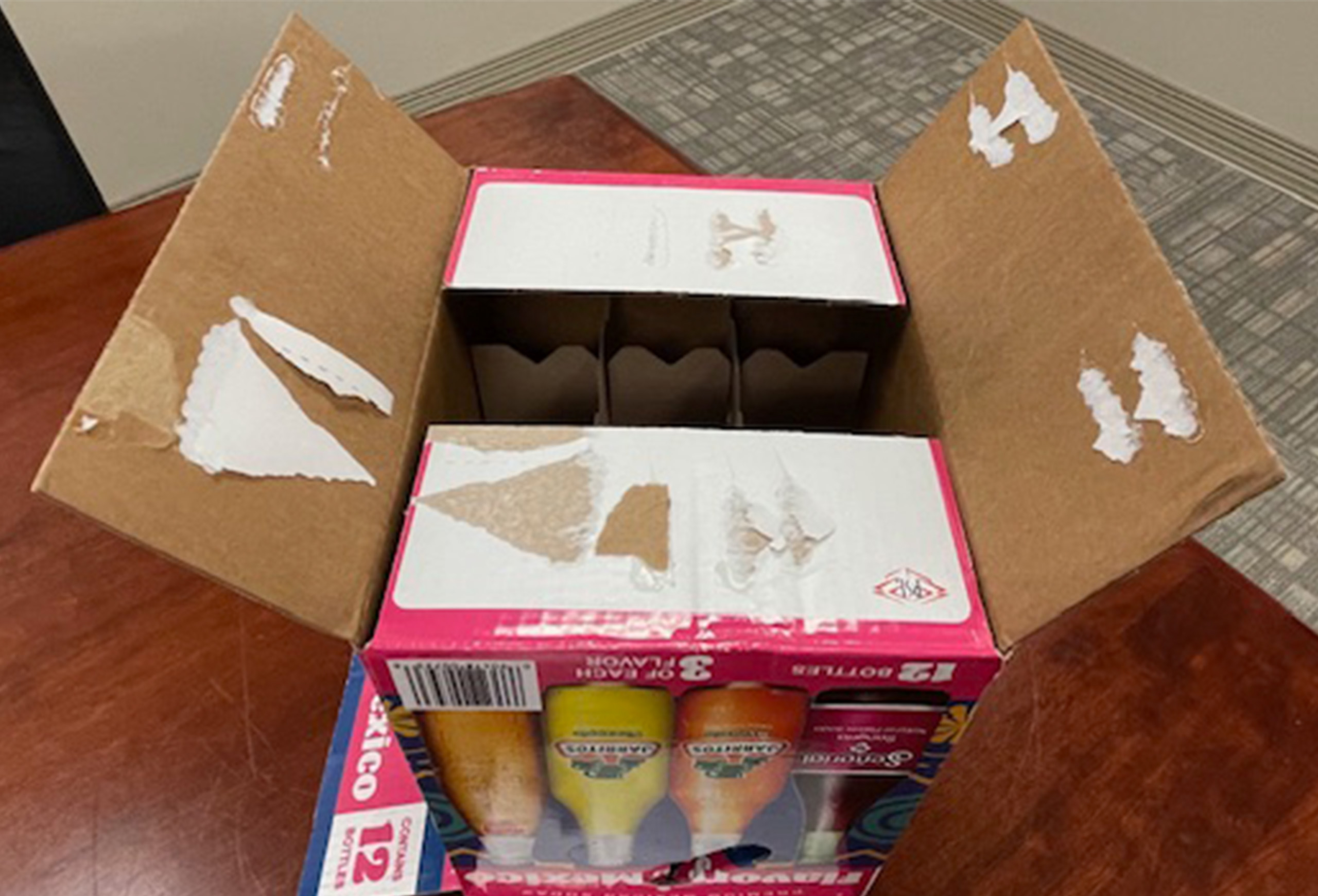
The day started with a daring expedition into the heart of the mundane, a place where the extraordinary awaits in the most unexpected places… the grocery store. Stealthily navigating through aisles of canned goods and shelves stacked with jars of ooey gooey goodness, our senses heightened, ready to detect any signs of adhesive anomalies. It was here that we spotted our intended target. Little did we know that purchase would bring us face-to-face with something frequently experienced but rarely understood by the untrained eye: a glue fail.
Once home, we excitedly unloaded the box, ready to delve deep and enjoy the bottles of the tasty beverage it was tasked to safeguard. With bated breath, we pulled the first flap away and a hush fell over the room. Lo and behold, the inside of the flap exposed failed glue bonds. In that moment, time seemed to stand still as we found ourselves mere inches from an adhesive failure.
A Closer Look at the Glue Fail
As the sun began its descent over the horizon, we continued our observation of the box and considered the reasons this box suffered a glue-fail fate.
With closer inspection of the flaps, it was clear that only one section of the adhesive successfully bonded. This was uncovered when a fiber tear was visible on one of the flaps. One reason for this adhesive failure is a lack of compression. During the manufacturing process, a box usually travels down a line, being filled with its intended contents, having adhesive applied, and then undergoing compression to ensure the glue successfully bonds to keep the boxes contents sealed tight and safe. If there is a problem with the compression machine or the compression is not properly set, this can lead to a failed bond and a box with its flaps shamelessly gaping wide open. Without knowing the type of machine, it’s hard to say whether this was the cause of the glue fail.
Another possibility is that the adhesive applied to the box wasn’t hot enough. Even with the right amount of compression, glue that isn’t the right temperature will not bond properly. This again is because of incorrect machine settings.
The last cause of the glue fail we considered can’t really be considered a glue-failure, as it’s not totally the glue’s fault. When a corrugated box is produced, it’s most often the brown color visible on the inside of the box. From there, it may have a white coating applied before another image is printed. Some boxes have a clear coat applied as a final layer to keep whatever imagery printed on it safe from chipping, scratches or any other damage. When a clear coating is applied, it makes the surface of the box smooth, and a special type of adhesive should be used to seal the box. If a special type of adhesive isn’t used, the area where the flaps will be sealed should be a “blanket area,” meaning the clear coating should not be applied in that area so the surface remains rough, and the adhesive can bond properly.
With a visual inspection, we noticed that all the flaps appeared shiny. They also had a smooth texture which usually means a clear coating was applied. Like the possibilities mentioned before, it’s hard to say what caused this glue-fail without knowing the type of adhesive that was applied. Maybe a special adhesive for clear-coated boxes was used but it wasn’t hot enough or there wasn’t compression during the manufacturing process.
The Adventure Comes to an End
As we bid farewell to the box and left it to carry on in its journey through the recycling process, we vowed to carry forth the memory of our encounter. For in the unpredictable moments of glue failures, there is always a silver lining – a learning -waiting to be discovered, if only we have the courage to look.
If you experience a glue fail or a glue-mergency, give Chicago Glue & Machine a call. We’re here 24/7/365 for any adventure that comes our way!