CASE STUDY: A Solution to Downtime, Adhesive Waste, and Unexpected Expenses
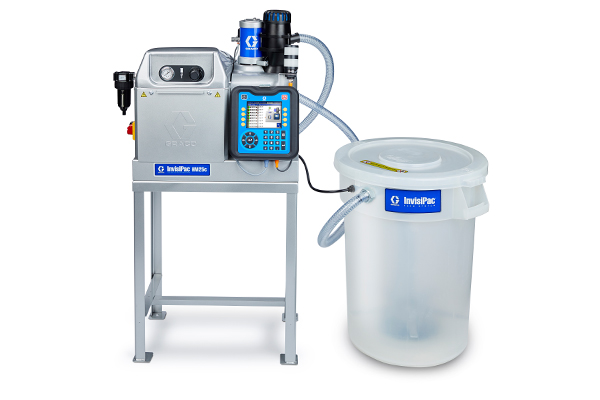
Challenge
Imagine it’s your first day at your new job as Maintenance Manager at a food supplier in Wisconsin. Not only are you working hard to get a lay of the land, but your production line has been ripe with challenges for months. Adhesive lines are frequently clogged due to charring and plugged applicator filters need to be changed every two weeks. This downtime on the production line is costing the company not only time, but money. You find out that your team is running through two skids of glue per month. Something has to change, so you get ready to roll up your sleeves.
This is the situation that the Maintenance Manager at Gold Standard Baking, found himself in earlier this year. And as he became more integrated with his team and the production line, he found that a brand-new piece of equipment was sitting in the plant. He realized that the emails, texts and voicemails he’d been receiving from Francisco Miranda at Chicago Glue & Machine were in reference to this equipment. What he thought was a sales pitch was actually a request to meet to discuss how to implement this new machine into his operations. It was the last thing he wanted to take on at the time, but he decided to return Francisco’s call to learn more.
Solution
Francisco started engaging with Gold Standard Baking, he shared with him the challenges he was facing as the new Maintenance Manager. Not only was the production line downtime a huge issue, but his team was wasting a few hours each week (an hour and a half each morning) waiting for adhesive equipment to heat up. Francisco listened to his concerns and then told him that the machine in his plant – the InvisiPac System – was the answer to all his problems.
If you were the Maintenance Manager would you believe it? At first, he was not convinced. He felt that the equipment was more than he needed and not worth the investment. But as he heard more about the unique features of the InvisiPac and felt the pressing need to reduce downtime and improve plant efficiency, he decided to give the InvisiPac a try.
Francisco recommended a six-week trial of the InvisiPac System, all but guaranteeing that he would be impressed with the results and move forward with purchasing the equipment.
Results
After four months of using the InvisiPac, he became a believer. He estimates that 30% of his time used to be spent worrying about Gold Standard’s glue system. Now with the InvisiPac, he only spends 1% of his time even thinking about glue. He discovered that the InvisiPac is a maintenance-free and carefree system that saves time and money.
- COST SAVINGS
The InvisiPac’s performance resulted in excellent glue savings. So far, Gold Standard has seen between 30-40% of glue savings per month and they are using two skids of adhesive every six to eight weeks (compared to four weeks prior). This is due in part to the InvisiPac’s tank-free system which eliminates excess glue spillage. He expects that the financial investment in the system will pay off within a year or less.
- TIME SAVINGS
The startup time of the InvisiPac is just 10 minutes compared to the hour that other machines often need. That means that the InvisiPac can be turned on right before production starts, no time wasted. The InvisiPac also eliminates the need for purging old glue from the nozzles each morning due to the elimination of charred glue.
- HEALTHY EQUIPMENT
Gold Standard’s biggest pain point, downtime, it is now a thing of the past. And filters only need to be changed once per quarter rather than every two weeks. Previously, the glue pot needed to be cleaned frequently because foreign material would easily find its way into the tank. But now, the InvisiPac keeps foreign material out thus keeping manual maintenance low.
Looking Ahead
In the future, Chicago Glue will conduct quarterly reviews of Gold Standard’s operations to ensure that their adhesive equipment is running properly and that their adhesives are performing well for their specific application.
The Maintenance Manager says, “Chicago Glue’s customer service and response time is second to none. They are very involved in every step of the process and always call or stop by to check in on us. That’s important, especially when you’re investing so much in one piece of equipment. We know we have their support which makes it much easier.”
He has recommended that Gold Standard’s Chicago plant works with Chicago Glue to change out their entire fleet of machines and switch to the InvisiPac System – spreading the time and cost savings even further.
Chicago Glue & Machine would like to thank Gold Standard Baking’s partnership and contributions to this blog.
To discuss a solution to downtime, adhesive waste, and unexpected expenses that might work for you, contact Chicago Glue today!