3 Steps is All it Takes for CGM to Troubleshoot Your Production Downtime and Save Money
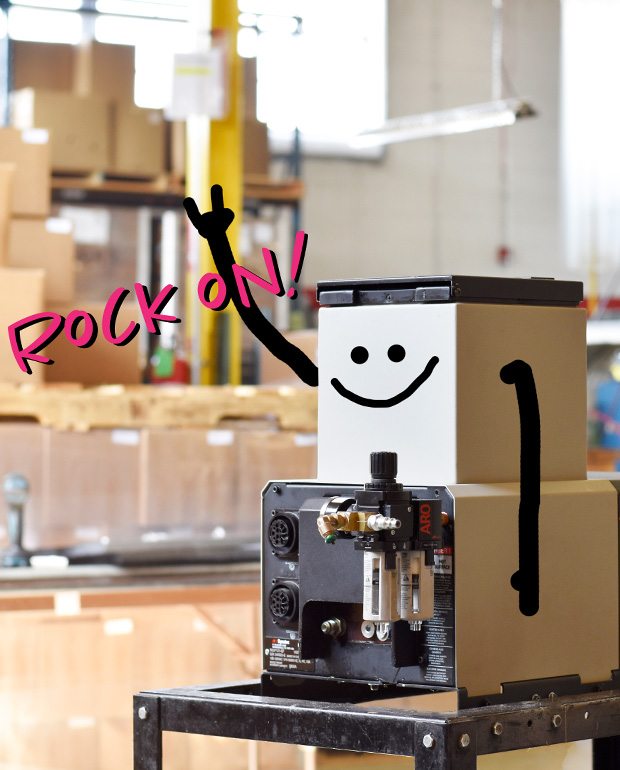
Have you asked any of these questions of your production lately?
Have you ever struggled to understand why more glue was used this month when your production was the same as last month?
Do you know if you are putting down the correct amount of glue?
Are your operators changing settings and potentially adding more glue because they think more is better?
All these questions and more can be answered by scheduling a baseline audit. Our process will give you accurate information with documentation on how much glue your production lines are using per piece. It also provides detailed information on the condition of your hot melt equipment.
1. First, we will work with your QA Department to understand the parameters of what is considered acceptable or unacceptable.
2. We will then schedule a meeting with your decision-making team to go over our findings and propose potential solutions to optimize your adhesive applications and reduce production downtime.
3. If you approve our proposal, we then work with your maintenance and production teams on the implementation of these changes and provide training to help ensure these changes last.
Your production lines are the heartbeat of your business and we want to help you ensure that they are performing at the highest efficiency possible. Please contact us at 630-250-0700 or [email protected] to schedule an appointment and help decrease production downtime.