Preventative Maintenance
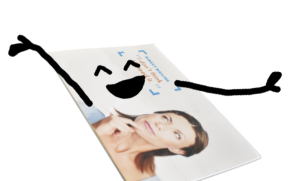
It’s our mission to make sure you never find yourself in a world without glue. And that’s where preventative maintenance services come into play. The best way to avoid the cost and hassle of a “glue-mergency” is by enrolling in our regularly scheduled preventative maintenance program.
Our goal is to find ways to prevent future issues with your adhesive and adhesive equipment by implementing a proactive action plan. And to help ensure you never miss a production day, we perform our on-site preventative maintenance services during scheduled downtime or a shutdown.
Does your production line often stop due to issues with your gluing equipment? And after your maintenance team inspects the situation, do they often discover something as simple as clogged nozzles? What if instead of dealing with clogged nozzles your system was routinely inspected and cleaned to identify and eliminate the root cause? How much time and money would that save your company?
Through our custom-designed preventative maintenance services, we can help you prevent issues like this and more, including:
- Equipment breakdowns that lead to overtime costs
- Equipment failures that lead to team member injuries
- Part failures that lead to expensive repairs and replacements
- Equipment malfunctions that lead to faulty end-products
- Equipment glitches that lead to missed deadlines
- Adhesive failures that lead to production downtime
Our preventative maintenance services have proven to significantly reduce and in most cases eliminate the annoyances of clogged nozzles and other maintenance issues that frequently impact hot melt systems. To get started, we recommend scheduling an adhesive and/or adhesive equipment audit with our team to assess the current state of your operations. From there, we can work together to create a proactive plan that is tailored to your facility and equipment.